扫码下载APP
找钨钼 上钨钼云商
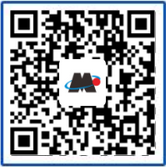
作者:钨钼云商 发布时间:2019-03-12 点击量:2582
油气工业目前仍然是高强度低合金钢最重要的应用领域,但汽车行业、海上与陆上工程结构领域目前也大量使用高强度低合金钢。
目前的高强度低合金钢金相组织有传统的铁素体-珠光体、贝氏体、马氏体和多相组织。每一种都有热轧和冷轧产品。当今的高强度低合金钢的屈服强度从260MPa 到1000 MPa以上不等。
当要求屈服强度必须超过550MPa,或要求特殊的金相组织时,需要在高强度低合金钢中添加钼。钼对于贝氏体(针状铁素体)和多相组织(常见于双相钢、复相钢或TRIP 相变诱导塑性钢中)的形成特别有利。
热机械轧制工艺及铌(Nb)、钒(V)和钛(Ti)微合金化元素的采用这两项技术进步,使HSLA钢在大口径管道中的成功使用成为可能。由于这些技术进展,可以生产制造出更高强度的钢而不需要成本高昂的额外热处理。 早期的HSLA管线钢管通常依靠减少珠光体 - 铁素体金相组织来使管线钢达到X60和X65。 但是更高强度的管线钢需要采用新的工艺路线和新的化学成分等不同的方法来实现。 20世纪70年代和80年代早期的广泛研究,采用各种Mo-Nb组合的化学成分,成功地开发出比X70更高的强度。 随着加速冷却等新工艺技术的引入,可以通过更简洁的无钼钢种设计,开发出更高的强度的钢种。
主流HSLA管线钢通常碳含量为0.05-0.09%,锰含量高达2%,及少量(通常最多0.1%)的铌,钒和钛的组合。该材料的优选生产路线是热机械轧制,最大程度使晶粒细化,从而改善机械性能。 晶粒细化是唯一同时提高强度和韧性的强化机制。
然而,由于许多轧钢厂终轧后无法采用所要求的冷却速度,甚至没有所需要的加速冷却设备,唯一可行的解决方案是选用合金元素如Mo来获得所希望的材料性能(见表1 和2)。并且,随着X70成为现代管线项目的材料主力和螺旋焊管的日益普及,在过去的几年中,对炉卷轧机(Steckel轧机)或传统的带钢热轧机(HSM)所生产的高性价比厚钢板和热轧卷的需求显著增长。因此,许多钢厂为满足当今日益增长的管线需求,重新引入并利用1970年代取得的冶金学成果,采用钼合金化。
表1 含Mo的X70-80管线钢
表2 含Mo X70和X80管线钢的典型化学成分
未来长距离输气管道一个明显趋势是向更高输送压力方向发展,这要求钢材具备X80的特性或更高的性能。 钢铁生产商正在这方面取得良好进展,特别是对于厚断面热轧带钢。 这里钼的回归发挥了重要作用,添加0.1%--0.3%的钼,不仅有助于生产晶粒度非常细的结构,而且还大大增强了微合金元素所带来的析出硬化效果。 此外,钼合金化帮助促进屈服曲线的连续并避免所谓的包辛格效应,这对于采用基于应变的设计规范很重要。
图1 19mm热轧钢板的抗拉强度与钼含量的关系
中国已建成的第二条西气东输油气管道横跨近5000公里,大规模采用了具有针状铁素体金相组织的X80级管线钢。 大部分管线采用热轧厚(18.4 mm)钢带制成的螺旋焊管。 管道材料为低C(<0.07%)、含Nb(0.07-0.10%)和Mo(0.2-0.3%)钢。 即使合金含量很低,最终的成品管道也含有大约10,000吨的钼。
有一种观点认为钼合金化会导致成本劣势,但经过全面的成本效益分析,可以证明这种观点是错误的。将常用的NbV微合金化X70钢与当今先进的低碳 NbMo钢相比较,后者的合金元素成本确实更贵。 但是,由于后者生产工艺效率更高,质量成本更低,因此基于热轧带钢的NbMo钢制造总成本更低。 此外,NbMo合金钢的加工制造如同X80。 在项目中使用X80而不是X70,需要的钢材更少,可以大大节省成本(参见图2和图3),因为材料成本约占管道项目总成本的30%。
图2 X70和X80管坯的生产成本结构(基于2007年平均铁合金价格)
图3 在固定输送压力下,长250公里、直径48英寸管道的钢材消耗量与强度等级的关系。
结构钢板的应用十分多样化,其整体趋势是向强度更高的厚板或特厚板发展。这样的话,即便最强大的冷却装置也可能会达到极限,因此钼合金化在此变得意义重大。如今,屈服强度高达700MPa 的厚板采用热机械轧制来生产,取代了较传统和昂贵的淬火-回火工艺。根据不同的强度和韧性要求,必须采用不同的冷却方式如加速冷却(ACC)、强化加速冷却(HACC)或直接淬火和自回火(DQST)。在这种复杂的钢中,钼与其它合金元素如Cr和Ni、以及微合金化元素 Nb, Ti 及B等结合,形成贝氏体或针状铁素体等具有极细晶粒尺寸的金相组织。有了高强度钢,可以采用较薄的板制造结构部件,这样可节约材料,降低运输、吊装和焊接成本。
传统的高强度低合金结构钢在常温下有良好的强度,但在高温下会严重地软化,因此它们不适合在比环境温度高得多的温度下使用。当建筑发生火灾时就会出问题。如果火灾下钢结构软化,则结构会在其自重下坍塌。所以耐火钢必须能抵抗大约400-700°C 温度区间的热激活变形(蠕变)长达若干小时。
在日本,钢在600°C时必须保持强度最低为所规定室温屈服强度的2/3,才被认为具有耐火性能。与普通碳钢相比,添加了Nb、Mo、 V和/或 Ti 的HSLA钢在高温下具有较高的强度,其中,MoNb合金钢(Mo含量高达0.6%)表现最佳。Mo通过铁素体的固溶强化和 Mo2C 颗粒的二次析出使钢强化。Nb 使晶粒细化,形成NbC析出相,进一步增加强度。此外,Mo 在NbC与基体界面偏聚可抑制NbC析出物的粗化。
与其它行业相比,汽车工业对轻量化的追求要强烈得多,这带动了钢铁行业前所未有的创新,以便能生产出具有高强度和良好冷成形性的合金材料。当今,乘用车的车身采用高强度钢的比例可高达80%,其中大部分是传统的(铁素体,铁素体 - 珠光体或贝氏体)高强度低合金钢,多相钢的比例不断增加。成熟钢种的抗拉强度可达1500MPa,新开发的牌号可达到2000MPa。在屈服强度超过700MPa的汽车用钢中,Mo合金化有其重要作用。Mo促进了贝氏体金相组织的形成,其具有比铁素体- 珠光体金相组织更高的强度。这些贝氏体钢对于结构加固件,车轮,底盘零件和卡车车架特别有用。 Mo与Nb和Ti等微合金化元素的协同作用也引领了超高强度铁素体钢的发展,这些钢的强度是通过大量沉淀硬化获得的。Mo在这些钢中的作用是多方面的:
Mo在热机械轧制期间延迟了微合金化元素的析出;
Mo在热轧过程中通过晶界的溶质拖曳延迟了再结晶;
Mo延迟了从奥氏体到铁素体的转变,从而产生更细的晶粒尺寸;
Mo可防止铁素体中析出的细小NbC或TiC颗粒的粗化(奥斯特瓦尔德熟化)(图4)
图4 添加Mo对铁素体中Ti/Nb碳化物析出的抗粗化作用
多相钢如DP(双相)、TRIP(相变诱导塑性)和CP(复相)钢可以直接利用轧制热量或通过采用额外的热处理(通常在冷轧后)来生产。 后者通常是汽车用钢常规的做法。 Mo合金化的主要作用是改变CCT曲线中的相区,相区规定了转变冷却速率的处理窗口,从而最大程度地减少了最终带材产品的性能变化。
对于轧制态的双相钢,在最终淬火将剩余的富碳奥氏体转变成马氏体之前,冷却模式必须能够形成足够的先共析铁素体基体而不使珠光体成核。 这通常在两步冷却过程中实现。 Mo对珠光体“鼻子”有明显的影响,非常有效地延缓了珠光体的形成。 它对先共析铁素体反应的延迟作用小得多,因此大大增加了所允许冷却速率的窗口区间并使生产过程更加稳健。
对于冷轧带钢,可通过Ar1和Ar3温度之间的临界区退火来调节多相显微组织中的铁素体量。 新形成的奥氏体部分在处理期间富含碳,之后在连续退火线(CAL)或连续镀锌线(CGL)中,在足够高的冷却速率下转变成马氏体。 Mo合金化降低了产生完全马氏体转变所需的临界冷却速率。 因此,仍然可以使用并非专门用于生产DP钢的CGL,这样,钢厂对生产的规划和安排具有更大的灵活性。
TRIP钢临界区退火之后并不立即淬火至马氏体转变温度以下,而是在中间温度下形成不含碳化物的贝氏体。 在该温度下保持一段时间后,不含碳化物的贝氏体转变成残余奥氏体和贝氏体铁素体。 钼使这种贝氏体转变极为缓慢。 如果保温时间较长的话,可以获得TRIP辅助的DP钢。 减少贝氏体区域的保持时间可得到DP钢,这是优先转变成马氏体的结果。 添加Mo有助于在加工后获得较高的马氏体和较低的残留奥氏体含量,由此显著地提高了抗拉强度,且不会对焊接性能造成太大的影响(就碳当量而言)。
当无碳化物的贝氏体分解成残余奥氏体,马氏体和贝氏体铁素体等若干组织成分时,则获得了复相(CP)钢的显微组织。 马氏体组织提高了抗拉强度,贝氏体铁素体提高屈服强度,残余奥氏体组织提高延伸率。
通常的Mo合金化HSLA钢表现出优异的冷成形性能,下图为测试样品表现及利用了上述优良性能的汽车部件。其中左上为多次弯曲(“手帕”)测试, 右上为扩孔试验。左下为高度变形的悬架臂, 右下为成型车轮。
上一篇:不锈钢在结构上的应用
下一篇:双相不锈钢焊接的通用准则